Your challenges
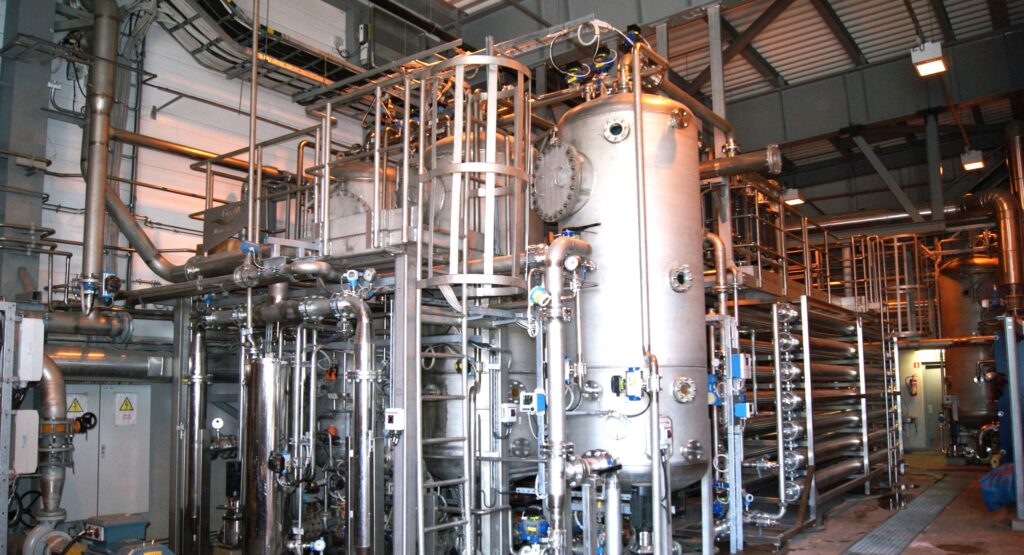
Consistent ultrapure water quality is essential for plants to protect high-pressure boilers, maximize thermal efficiency and meet sustainability and compliance targets.
Challenge 1: Protecting boiler systems from scaling and corrosion
High-purity water is essential for steam generation. Even trace levels of dissolved salts or organic matter can damage turbines, boilers, and piping, leading to costly downtime and maintenance.
High-purity water is essential for steam generation. Even trace levels of dissolved salts or organic matter can damage turbines, boilers, and piping, leading to costly downtime and maintenance.
Challenge 2: Optimizing water reuse and minimizing waste
Reusing condensate and flue gas recovery streams can reduce water intake and improve overall efficiency, but only if contaminants like silica, organics, and hardness are reliably removed.
Challenge 3: Ensuring consistent performance under variable conditions
Feedwater quality and flow often fluctuate, especially with seasonal or load-based changes. Treatment systems must adapt while maintaining high recovery and consistent output quality.
Our demineralization solutions
We provide complete, high-performance demineralized water solutions engineered for the most demanding steam and heat applications. Whether you need to protect high-pressure boilers, polish return condensate, or treat complex flue gas condensate streams, our technologies deliver reliable water purity, operational efficiency and long-term plant protection.
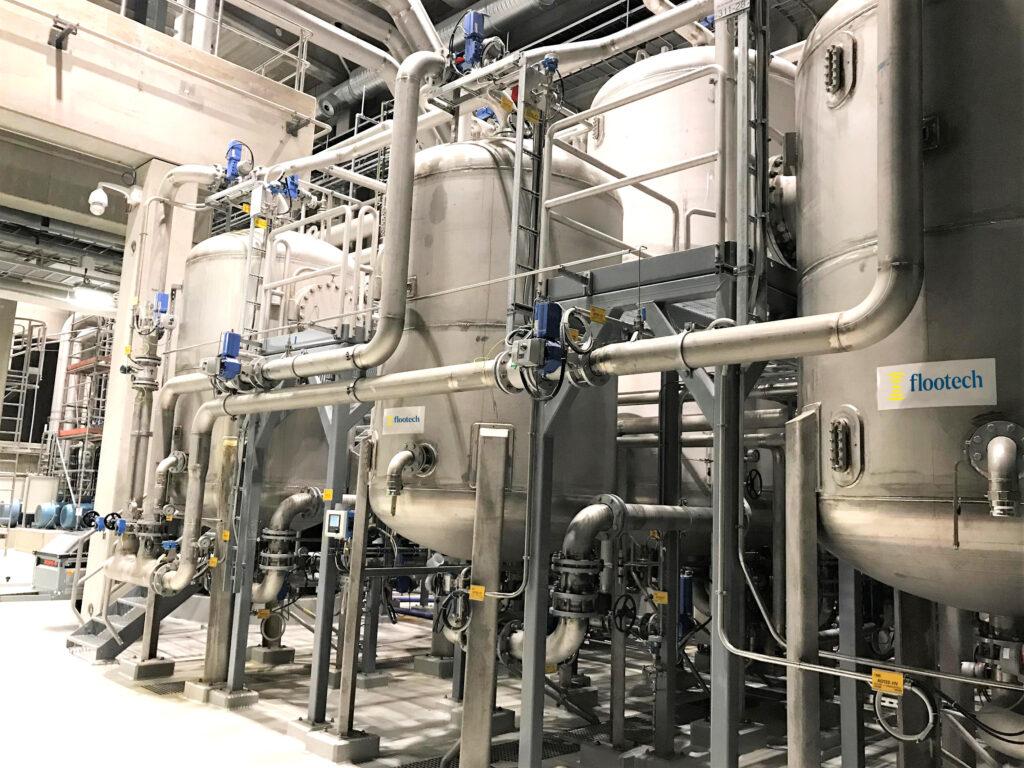
Boiler Feedwater Treatment
Our FlooIX™ (ion exchange) and FlooRO™ (reverse osmosis) systems are designed to work alone or in combination to remove dissolved salts, silica, hardness, and organics from make-up feedwater. FlooIX offers proven, high-capacity ion exchange with customizable resin beds, while FlooRO delivers compact, energy-efficient removal of even the finest impurities - ideal for high-pressure boiler applications. Together, they ensure minimal scaling, corrosion, and downtime across the steam cycle.
Condensate Polishing
We offer advanced polishing systems using mixed-bed ion exchange and filtration technologies to remove ionic and particulate contamination from return condensate. These systems extend the life of your equipment by maintaining ultra-low conductivity and silica levels, supporting the safe reuse of condensate in high-purity steam systems.
Flue Gas Condensate Treatment
Our treatment solutions for flue gas condensate are tailored to remove acid gases, metals, organics, and fine particles from this aggressive water stream. By integrating pH neutralization, ultrafiltration, and deionization steps, we enable safe discharge or reuse, helping you recover water and energy while meeting environmental regulations.
Special Industry Applications & Experience
We offer a broad range of filtration, ultrafiltration, softening, and deionization technologies to meet the specific purity requirements of your plant. Trusted across a wide range of industries that rely on steam and heat systems - including pulp & paper, energy, food & beverage, and chemical processing. Whether you're running high-pressure boilers, cogeneration plants, or complex heat recovery systems, we deliver water quality and operational reliability that meet your specific demands.
Our technology company Flootech brings decades of experience and deep industry knowledge, with a strong track record especially in the pulp & paper and energy sectors. With numerous successful demineralized water plant installations and long-standing partnerships, we understand the operational pressures and purity standards required to keep your processes running at peak efficiency now and in the future.
Customer benefits
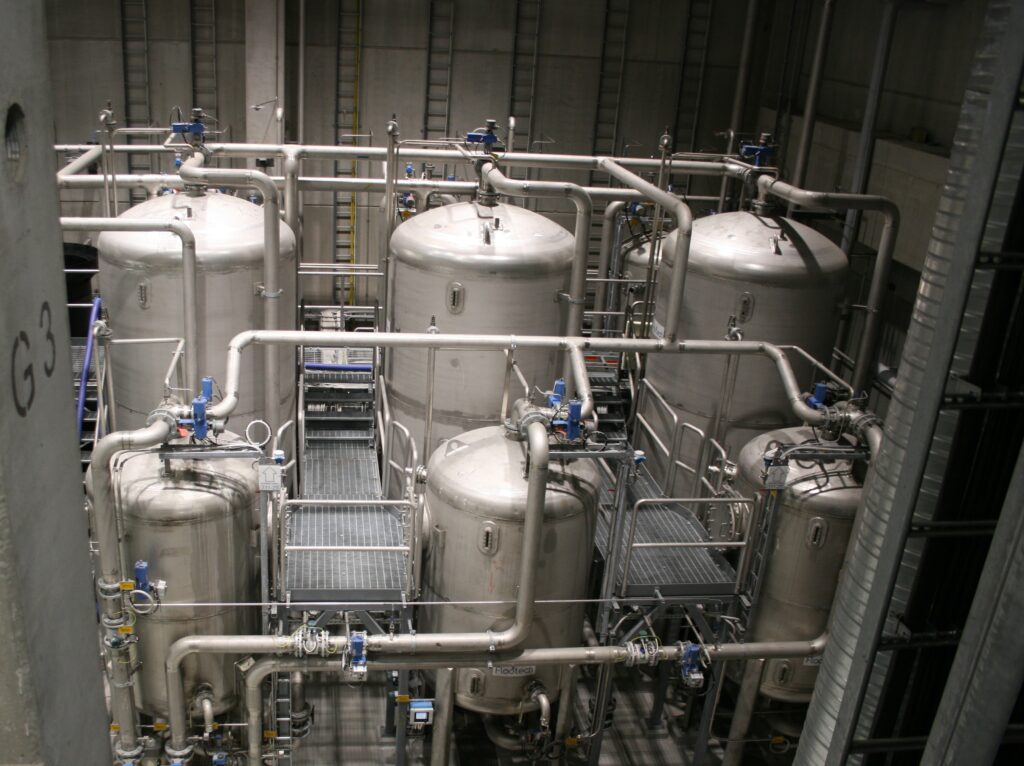
Our membrane systems are engineered for performance, uptime, and water circularity. Whether you’re upgrading an existing plant or building new, we help to make your water-cycle future-proof.
-
Protect steam systems with consistent high-quality water to reduce scaling and corrosion.
-
Lower OPEX through high recovery rates and efficient chemical and energy use.
-
Ensure water quality with low conductivity and silica, even under variable conditions.
-
Achieve compliance with strict purity and environmental standards.
-
Integrate and expand easily with compact, modular, and automation-ready systems.